Artificial Intelligence Shapes Future Acura RSX Specifications
Artificial Intelligence Shapes Future Acura RSX Specifications - The RSX Nameplate's Electric Crossover Plot Twist
The Acura RSX nameplate is indeed making a comeback, though not in the form many might remember. The revival sees the once sporty coupe transformed into an electric crossover, a significant shift in identity. This new direction positions the RSX as a key player in Acura's push toward electrification, set to be among the initial vehicles built at Honda's new dedicated North American EV production facility later this year. While the nameplate historically evoked a specific kind of compact performance, its application to an electric crossover raises questions about how the brand will translate that legacy into this new segment and powertrain, fundamentally altering expectations for its return.
This iteration of the RSX, arriving as an electric crossover, presents some intriguing technical points beyond simply repurposing a familiar nameplate onto a different vehicle type. From an engineering perspective, there's attention given to fundamental aspects of the electric platform. For instance, the battery pack appears designed not just for energy storage but as a contributing structural element, integrating the cells directly into the chassis architecture. This structural role is intended to bolster torsional rigidity and could influence crash energy management – a common strategy in newer EV designs, and one that's particularly relevant in managing the dynamics and safety of a taller vehicle like a crossover while aiming for a lower perceived center of gravity.
Aerodynamic efficiency is another area highlighted. Given the range sensitivity of EVs, optimizing airflow is paramount. The approach here seems to involve not just passive body shaping but also active elements like adaptable grille vents and potentially variable ride height at speed. While claiming an "exceptionally low" drag coefficient needs to be measured against peers in the segment, the deployment of such active systems, likely refined through extensive simulation (including AI-assisted methods), indicates a serious effort to reduce aero drag and extend operational range under varying conditions.
The powertrain architecture includes a dual-motor layout, and the adoption of silicon carbide (SiC) technology in the power inverters is noteworthy, aligning with current high-performance EV standards. SiC components handle higher voltages and temperatures more efficiently than traditional silicon, leading to more compact inverter designs, better power density, and lower overall energy losses – translating directly into slightly more power or range from the same battery pack. It’s an expected but welcome technical choice.
Thermal management of the battery system also seems to be a focus. A sophisticated, potentially algorithmically controlled system (referred to as AI-controlled) is mentioned, capable of pre-conditioning the pack for optimal operation or actively cooling it during high-speed charging. The aim is to maintain high DC fast charging rates for longer durations, minimizing the time spent plugged in compared to systems that significantly taper power early. This is a critical aspect for usability, although real-world gains depend heavily on charging infrastructure capabilities and environmental factors.
Finally, the vehicle's body structure utilizes a mix of materials – various grades of steel, aluminum, and potentially some composite reinforcement in specific areas. This multi-material approach is standard practice today, balancing strength, weight, and cost. While "generative design" is a term often used, the underlying principle is employing computational tools to determine optimal material types and placement based on simulated load cases for crash performance, stiffness, and manufacturing constraints. It’s a practical application of advanced design software to achieve a balance of competing requirements.
Artificial Intelligence Shapes Future Acura RSX Specifications - Under the Hood New Silicon and Software Systems
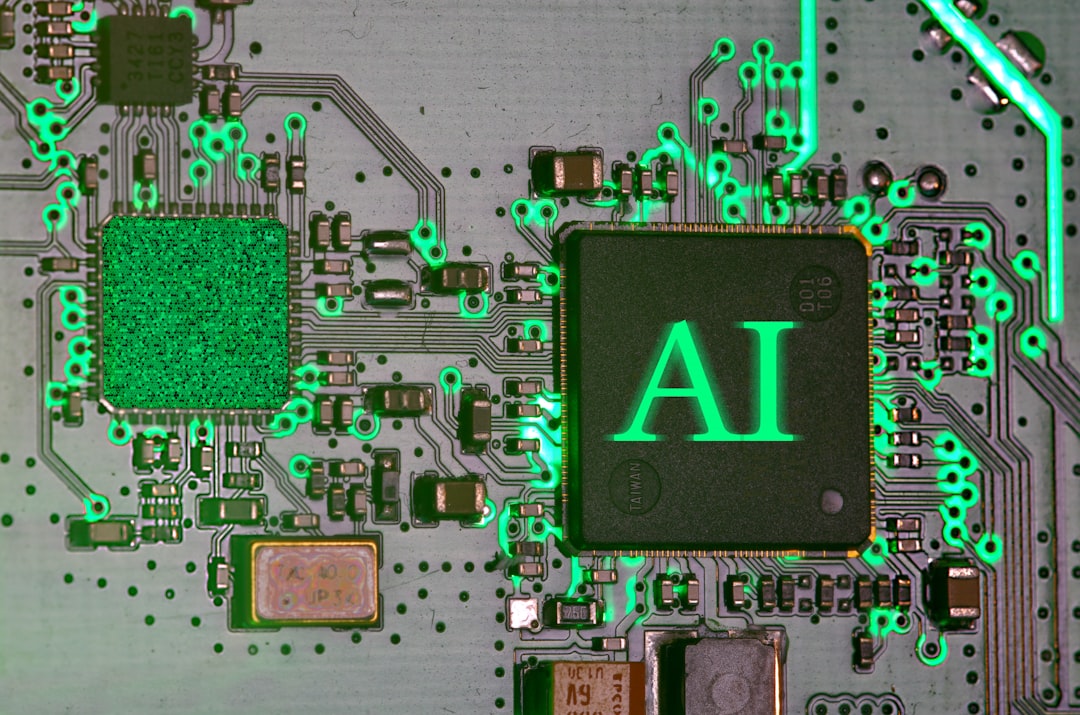
Below the surface of the upcoming Acura RSX's electric platform lies a significant focus on its core computational systems. This isn't merely an evolution of traditional automotive electronics, but rather a foundational shift driven by new silicon and advanced software integration. At its heart, expect to find specialized processing units designed to handle the complex demands of managing power delivery, processing high volumes of sensor data, and running the vehicle's numerous control algorithms – many now leveraging artificial intelligence techniques. The ambition appears to be creating a highly responsive and efficient digital architecture that underpins the car's dynamic behavior and energy management. While the specific performance gains depend on the effectiveness of this hardware-software co-design, the trend points towards vehicles becoming increasingly defined by the intelligence built into their foundational electronic systems.
The underlying electronic architecture for this RSX seems to represent the industry's accelerating shift towards fewer, more powerful computing nodes. Instead of a dispersed network of single-function microcontrollers, core processing is consolidated onto domain or zonal controllers leveraging new, purpose-built silicon tailored for automotive tasks. This architectural move significantly simplifies the physical wiring harness complexity across the vehicle—a practical engineering advantage in terms of weight reduction, manufacturing ease, and potentially fewer failure points—while simultaneously placing heavy demands on the software layer for coordination and data management.
These new silicon platforms reportedly enable more advanced software functions. The discussion mentions AI algorithms analyzing real-time driving dynamics, traffic conditions, and navigation data to predictively optimize powertrain energy usage. While conceptually sound for potential efficiency gains by anticipating road conditions, demonstrating significant, consistent real-world benefit from such complex predictive control compared to robust reactive systems remains an ongoing challenge, heavily reliant on data quality and validation across diverse driving scenarios.
Furthermore, the vehicle's central control software is described as fully leveraging the high-frequency switching capabilities inherent in the SiC power inverters discussed earlier. This is where the capability of the hardware enables more precise software execution; the ability to rapidly switch power allows for finer-grained, higher-frequency control over the torque distribution to each motor. If effectively implemented and tuned, this could translate into enhanced vehicle agility and stability through dynamic torque adjustments under various driving conditions.
Integration extends inward as well, with onboard AI systems said to utilize sensor fusion—potentially involving cabin cameras or seat sensors—to identify specific occupants. The goal is apparently automatic application of personalized settings for environment, audio, and seating. While automatic profile loading is not entirely new, achieving *deeply* personalized settings reliably through sensor data fusion adds considerable complexity to the system design and raises typical considerations regarding data privacy and the potential for errors or unintended behavior in recognition and application. It highlights the trend towards vehicles becoming more integrated digital platforms, relying heavily on sophisticated software and sensor interpretation.
Artificial Intelligence Shapes Future Acura RSX Specifications - How Tech Interfaces Redefine the Cabin Experience
Modern vehicle cabins, like those anticipated in vehicles such as the updated Acura RSX, are undergoing a transformation driven by advanced technology interfaces. Systems increasingly employ artificial intelligence for critical functions, such as monitoring driver state to identify signs of fatigue or inattention, aiming to bolster occupant safety and overall comfort. Beyond safety, the cabin experience is being redefined by features enabling deeper personalization, potentially recognizing individuals through methods like biometrics and automatically adjusting environmental controls, audio preferences, or seating positions. While promising enhanced convenience and a tailored environment, these integrated systems also bring challenges, particularly concerning the privacy of occupants' data and the critical need for these complex technologies to function flawlessly and reliably in real-world scenarios. As cars evolve into sophisticated connected digital spaces, the interaction experience within the cabin will be shaped by this ongoing effort to integrate advanced computing and sensor technology, requiring a balance between high-tech features and maintaining an intuitive, focused connection to the journey itself.
One area where computing power increasingly shapes the experience inside the cabin is through how users interact with vehicle systems. Rather than fixed displays and physical controls, the focus shifts to interfaces that attempt to adapt and integrate information more dynamically, driven by advanced software and sensing.
Advanced computational processing within the cabin system aims to interpret the context of the driving situation and the potential state of the driver. This information could theoretically be used to modify the layout and content displayed on screens or projected surfaces, prioritizing critical information during demanding conditions while allowing access to secondary functions when appropriate. The idea is to tailor the human-machine interface in real-time, though validating whether this actually improves driver focus or simply adds another layer of complexity is an ongoing challenge for system designers.
The displays themselves are evolving. Beyond conventional touchscreens, the integration of augmented reality principles means crucial data might be projected directly into the driver's view, appearing overlaid onto the physical environment. This could include information related to driver assistance systems, warnings about external hazards, or even guidance points derived from navigation. The goal is to place relevant data where the driver's attention is likely to be focused, although ensuring that such overlays are clear, unobtrusive, and remain accurately aligned under various lighting and environmental conditions requires sophisticated calibration and projection technology.
Interaction is also extending beyond visual and auditory cues. Sophisticated haptic feedback systems built into controls, touch surfaces, or even seating are being developed to provide tactile alerts or prompts. These physical cues could signify an impending safety system intervention, communicate navigation instructions directionally, or perhaps indicate system states without requiring the driver to shift visual focus. Effectively integrating haptics into the user experience means engineering responses that are distinct, intuitive, and not distracting, which can be a subtle design challenge.
Building on in-cabin sensing discussed previously, computational interpretation of cues like eye gaze, posture, or even potentially inferred physiological signals is being explored not just for identification, but to estimate a driver's alertness or stress level. The intent is to link these inferences to subtle adjustments within the cabin environment—modifying lighting color temperature, adjusting climate control flow, or altering audio characteristics—in an attempt to proactively support driver well-being. The reliability of accurately inferring internal states from external sensor data, however, remains a significant hurdle.
Furthermore, the digital display surfaces themselves are moving towards greater adaptability. The physical configuration or content partitioning might change based on the selected driving mode or detected situation—perhaps emphasizing dynamic vehicle data when driving actively, then transitioning to a more consolidated view focused on navigation and media playback during cruising. The feasibility of truly fluid, dynamic display areas could eventually rely on emerging flexible display technologies, but the software logic needed to manage these transitions seamlessly and reliably under all conditions is complex.
Artificial Intelligence Shapes Future Acura RSX Specifications - Tuning Performance Through Bits Not Gears
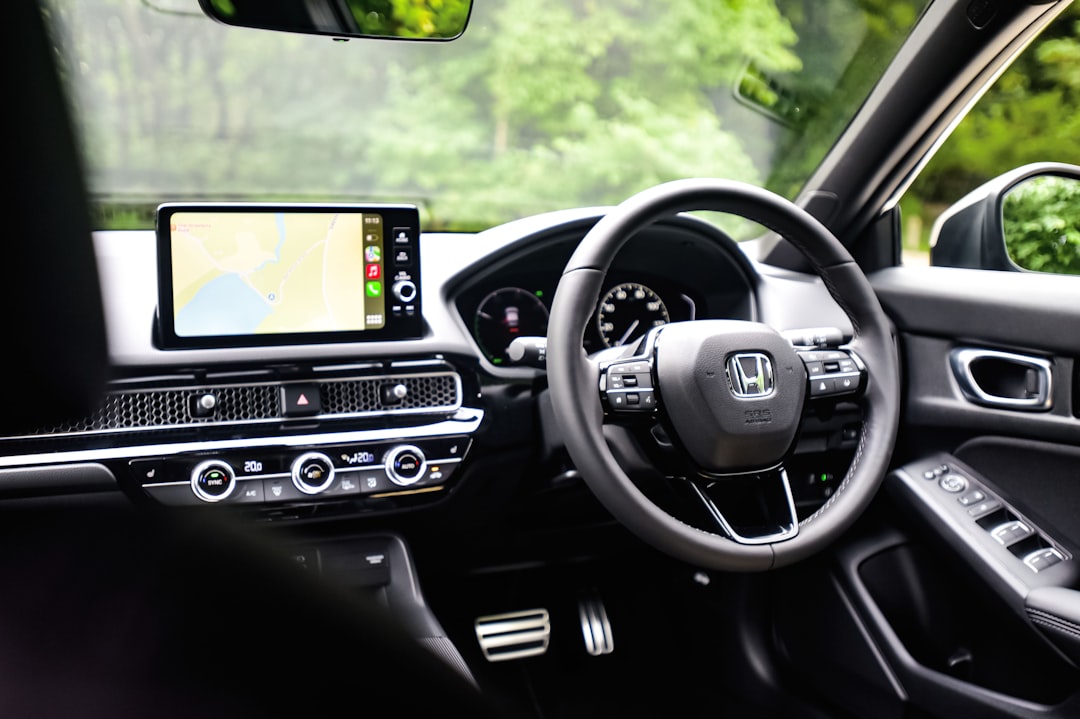
Moving beyond discussions of underlying hardware and software, the real impact on driving feel and capability increasingly comes down to what's being done within those systems – a shift away from purely mechanical tuning toward "tuning performance through bits, not gears." This represents a fundamental change in how vehicle dynamics and powertrain characteristics are defined and adjusted. Instead of swapping physical components, fine-tuning is achieved primarily through sophisticated software algorithms, advanced signal processing, and leveraging computational power, often including artificial intelligence routines, to constantly manage and optimize everything from power delivery and chassis responses to energy efficiency. This digital approach promises a level of precision and adaptability previously unattainable, enabling adjustments that happen microseconds faster than traditional methods. However, it also places enormous reliance on the robustness and accuracy of the code, and ensuring predictable, reliable performance across the infinite variables of real-world driving remains a significant engineering challenge. It's about executing performance directives via complex code running on specialized silicon, which changes the game significantly from turning wrenches or swapping parts.
While the fundamental physical platform of an electric vehicle sets its capabilities, an increasingly critical layer shaping performance is the software that orchestrates its behavior. This represents a shift where traditional mechanical tuning points—think gear ratios, differential characteristics, or damper curves adjusted physically—are being augmented or even replaced by algorithmic manipulation. It's about refining performance characteristics through computations and data, leveraging the precise control inherent in electric drivetrains.
The core technical enabler here is the ability to control individual motors with extreme rapidity and precision, building upon the high-frequency switching capability of components like SiC inverters. This allows software to dynamically adjust torque split, regeneration levels, and response curves across milliseconds. The ambition is to move beyond simply reacting to wheel slip or stability limits towards proactively shaping the vehicle's dynamic state based on sensor inputs and predictive models.
One intriguing aspect is the exploration of personalizing this software-defined performance. Concepts suggest systems that could analyze a driver's inputs during spirited driving sessions, learning their specific style and preferences for traits like initial turn-in sharpness, mid-corner balance, or braking feel. The software could then subtly adapt responses to better match that individual profile, essentially creating a continuously evolving, personalized tuning map. Furthermore, there's potential for the system to simulate mechanical sensations historically associated with combustion performance cars, such as the specific lock-up feel of a mechanical limited-slip differential or distinct engine braking characteristics, purely through intelligent manipulation of motor torque and regeneration profiles. It's an interesting technical exercise, though whether such simulations fully replicate the authentic feel remains a point of engineering inquiry.
This computational approach also opens the door for dynamic performance updates throughout the vehicle's life. The idea floats that analysis of anonymized driving data across a fleet could identify new tuning optimizations, perhaps related to thermal management under load or specific control strategies for certain maneuvers. These refinements could then theoretically be delivered to vehicles via over-the-air software updates, meaning the car's dynamic performance envelope might evolve and potentially improve over time, a stark contrast to the fixed characteristics of mechanically tuned vehicles.
Beyond dynamic handling, predictive software management extends to maintaining performance during sustained hard driving. AI systems are reportedly being tasked with analyzing not just current temperatures but anticipating heat buildup across motors, inverters, and battery cells based on driving intensity and environmental factors. The goal is to proactively adjust cooling strategies to prevent or minimize power derating, ensuring more consistent peak performance output during demanding conditions compared to purely reactive thermal management systems. This predictive calculus, using high-frequency sensor data to anticipate dynamic events or component stresses and adjusting controls milliseconds beforehand, represents the leading edge of attempting to shape performance at the limit primarily through bits, not traditional gears or mechanical adjustments.
More Posts from specswriter.com: